ROHM has developed DC/DC converter control technology featuring an ultra-narrow minimum pulse width of 9ns. Referred to as Nano Pulse Control, this technology enables direct conversion from 48V input to around 1V, even at a high switching frequency of 2MHz. By introducing a ‘flying start’ that obtains the coil current required for control in advance, ROHM was able to successfully reduce the minimum pulse width by two-thirds, from the previous 30ns to 9ns. (This article)
Initiatives to increase the supply voltage of communication/network devices, computers, and automotive electronics from the conventional 12V and 24V to 48V have been gaining momentum. Perhaps the greatest benefit of increasing the voltage to 48V is reduced power loss. Assuming the same power supply, doubling the supply voltage can reduce power loss generated in the supply circuit by as much as 75%.
However, this move towards higher voltage is not without its drawbacks. The biggest disadvantage is the additional number of voltage conversions required. Following advancements in production process technology, digital ICs such as MCUs, FPGAs, ASICs, and ASSPs are requiring lower supply voltages, to 2.5V, 1.8V, or even 1V. Increasing the supply voltage to 48V makes it increasingly difficult to directly convert to the low voltages required by digital ICs. It becomes necessary to utilize 2-stage conversion that first converts to an intermediate bus voltage of 9V or 12V (Fig. 1).
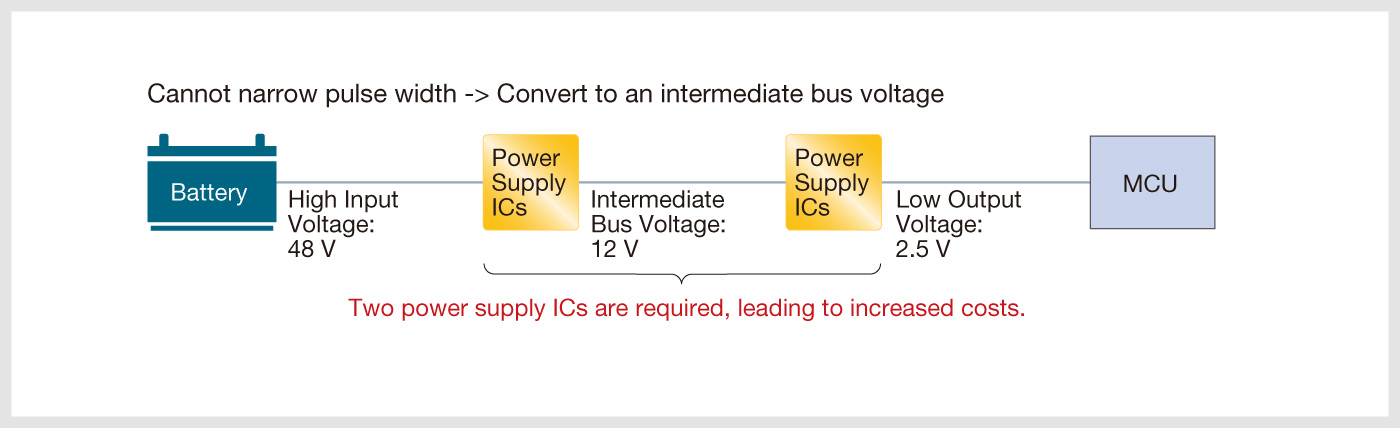
Figure 1. Stepped Voltage Conversion Required
Conventional automotive DC/DC converter ICs cannot directly convert 48V to 2.5V. As such, 2-stage conversion is needed using an intermediate bus voltage to achieve 2.5V output.
In general, performing voltage conversion results in power loss. In fact, increasing the number of conversion from 1 to 2 doubles the power loss. So even if the power loss is reduced to 1/4th by raising the supply voltage, the greater power loss incurred by increasing the number of conversions diminishes the benefits of switching to 48V. In addition, as 2 voltage conversion circuits are required, the number of components will also double, increasing component costs along with board area.
Direct conversion is not possible
To take full advantage of switching to 48V, it is necessary to be able to directly convert from a 48V supply to a low voltage such as 1V, 1.8V, or 2.5V in a single stage. Until now, however, this has been extremely difficult to achieve due to technical reasons. This is because the minimum pulse width of the PWM signal that controls the DC/DC converter (voltage conversion) circuit could not be reduced to the required level.
For example, assuming a direct conversion from 48V to 1V using a DC/DC converter circuit operating at a switching frequency of 2MHz, an extremely narrow minimum pulse width of around 10ns is needed. If the switching frequency is halved to 1MHz the minimum pulse width can be doubled, but would still be around 20ns.
Of course, decreasing the switching frequency even further will increase the required minimum pulse width even more. However, reducing the switching frequency demands larger external capacitors and coil (inductor) that increases the dimensions of the DC/DC converter circuit and creates additional problems
What's more, in automotive electronics it is necessary to avoid introducing noise into the AM radio band. The AM frequency band ranges from around 500kHz to 1.8MHz. So for practical purposes the switching frequency should be set to 2MHz or more. This means that to directly convert 48V to 1V a minimum pulse width of 10ns is needed. And converting to 2.5V requires a minimum pulse width of 25ns.
However, the smallest minimum pulse width on the market when ROHM began developing this technology was 30ns, which was the conventional limit. At the same time, the minimum pulse width of our standard products was 120ns, a long way off from 10ns (Fig. 2).
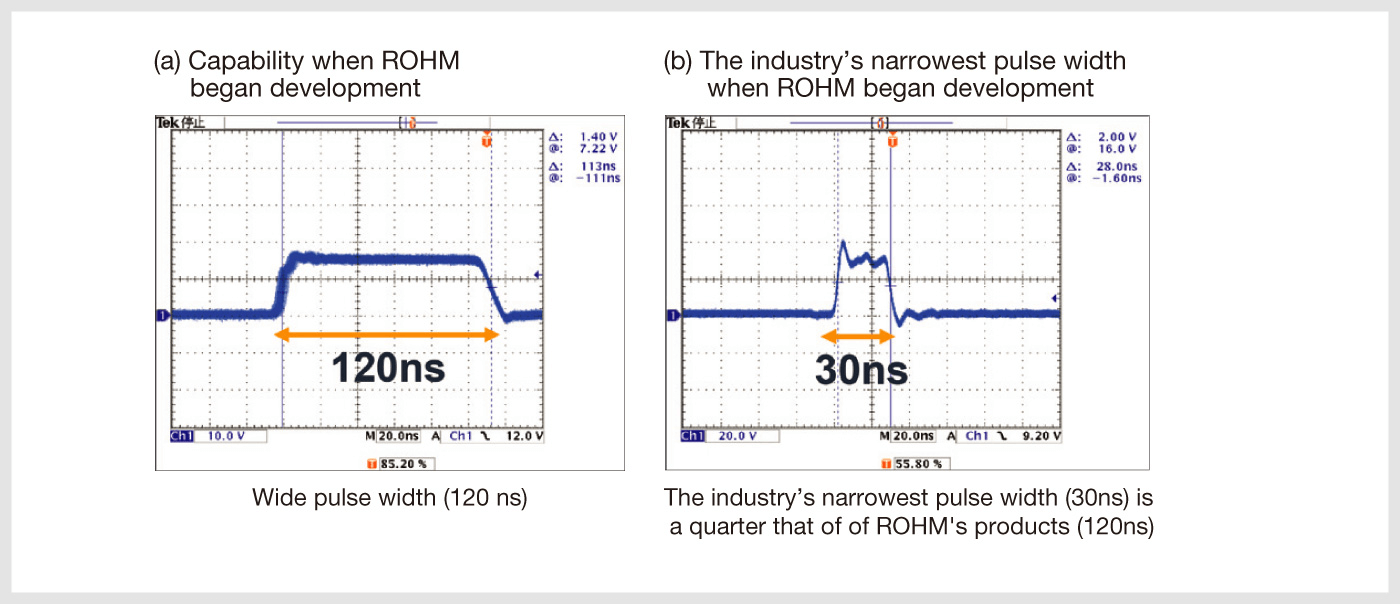
Figure 2. The industry’s narrowest minimum pulse width was 30ns
The figure at right shows the waveform of the narrowest pulse width in the industry (30ns). The left figure shows the minimum pulse width of ROHM products (120ns).
This is the biggest reason why direct conversion from 48V to 1V, 1.8V, or even 2.5V was not possible. There was no choice but to carry out 2-stage conversion utilizing an intermediate bus voltage of 7V, 9V or 12V.