Special Conversation on R&D
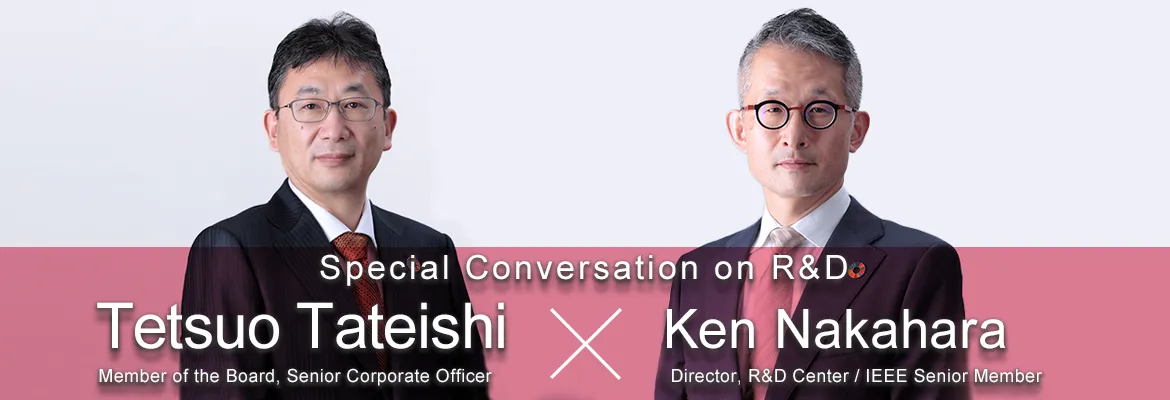
There will come a time when the products that are selling well now will eventually stop selling. The future of the company will be quite bleak unless the ‘buds’ of new products are born at that time. ROHM’s R&D Center is engaged in research and development to find the ‘seeds’ that will become the ‘buds’ of the next generation.
In this issue, Member of the Board Tetsuo Tateishi and R&D Center Director Ken Nakahara carry out a roundtable discussion on the ideal type of R&D. There are 3 themes. The first is initiatives for industry-government-academia collaboration, the second concerns ROHM’s R&D system, and the third covers features of ROHM’s R&D.
1.Initiatives for Industry-Government-Academia
-What to expect from universities. Pursuing things in greater depth and detail.-
The first topic of the roundtable discussion is the role of R&D in industry-government-academia collaboration. ROHM’s R&D Center has been conducting open research calls at universities, technical colleges, and public research institutions in Japan since 2016. Researchers and groups engaged in scientific and technological research are invited to apply for themes. The program supports activities by investing funds in a number of these themes, and results have already been achieved. So we asked Mr. Tateishi and Mr. Nakahara to discuss the purpose of the call to research, past results, and expectations for universities, technical colleges, and public research institutes.
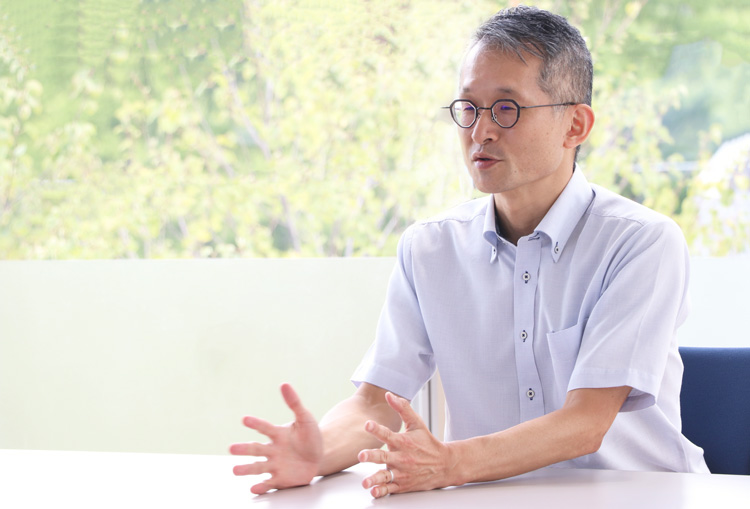
Tateishi:
I agree. As a company, commercialization is ultimately the goal. This is a given, and all of the knowledge that goes into a product needs to be widely understood. In contrast, in university research it is not necessary to know everything, but instead focus on one point and pursue it. As Mr. Nakahara pointed out, when a problem occurs with a product, it is important to dig deep into a single point and determine the cause. This ’digging deep’ experience expected from universities is what we would like to take advantage of.
Nakahara:
There are 3 situations in which we would like help from universities. The first is more in-depth knowledge and skills necessary to determine the cause and understand the essence of the problem, as already mentioned. Of course, deep knowledge is needed to create products as a company, and we are working on it at ROHM, but as Mr. Tateishi said, there is a tendency to focus more on the breadth of the product. This results in a lack of depth compared to university research, so we want to compensate for that. The second is a situation that temporarily requires specific knowledge or skills. University support is essential when short-term support for in-depth knowledge and technology are needed and which ROHM does not possess.
The third situation is one where the company does not have the means. For example, when we need to analyze something, sometimes a large synchrotron radiation facility such as Spring-8 may be required, but it is not easy to build such a facility in-house. This requires help from a university.
Calls for research continue to yield results
Nakahara:
In our open calls for research, we ask schools and research institutes engaged in research that matches ROHM’s current technological needs to apply.
Various results have already been achieved through R&D that was triggered by open calls for research. A recent example is joint collaboration with the Graduate School of Engineering at Osaka University. This research involves the world’s first successful transmission of uncompressed 8K video at full resolution using 300GHz terahertz waves. In addition to this, although we can’t go into details, there are other research results that are about to be commercialized.
Tateishi:
The amount of money earmarked for open calls for research in Japan is not large at 2.5 million yen per year (excluding tax). ROHM provides funds to start joint research. The research period is fixed, and if we can find mutual benefits during that period, we can proceed to the next stage.
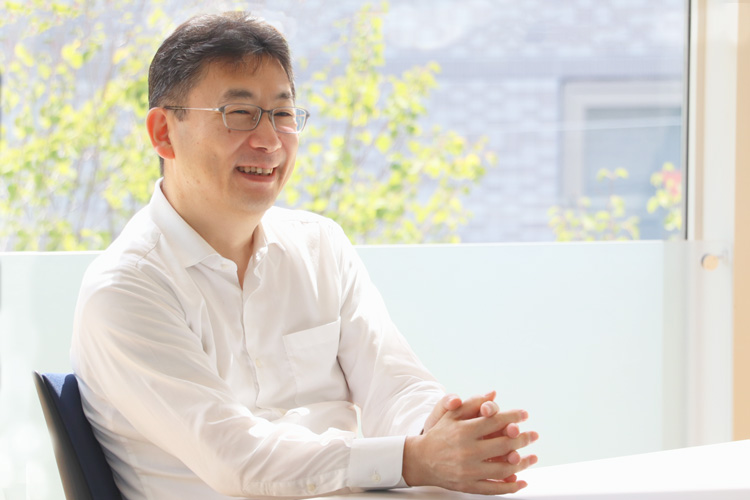
Experience stays with people
Nakahara:
I have a policy for conducting joint research with universities. When collaborating, it is important to assign a specific ROHM employee to be in charge and properly allocate both people and resources to the project. Surprisingly, this policy is not the norm, and in many cases it seems that companies simply provide research funding then just wait for the results. Since our aim is to deepen technology, ROHM places the utmost respect on university research. Unfortunately, however, sometimes research doesn’t go as planned, so we assign additional employees to learn what they can. Because even if the research doesn’t immediately lead to a product, the experience will remain and may be of help in the future.
Tateishi:
ROHM also does research on the same topic. Since we are a company, we have to incorporate the knowledge and technology created at universities into our products. And we are always looking into ways on how to incorporate it. ROHM’s call to research has produced numerous results by combining the in-depth exploration of technologies by universities with the exit strategies of companies. And we look forward to receiving more applications from various fields in the future.
2.ROHM’s R&D System
-Work on real R&D at ROHM-
In 2019 ROHM established a Specialist Position as a career path for engineers. This program is designed for those who wish to purse a single business in-depth, such as technology or legal affairs. On this topic, we asked Mr. Tateishi and Mr. Nakahara to discuss what they expect from human resources as it relates to R&D along with the background and purpose behind the introduction of the specialist position system.
Tateishi:
ROHM R&D is doing things differently, isn’t it? At the R&D Center’s debriefing session the question ‘What is the goal of this theme?’ was asked. This kind of comment is not normally made at debriefing sessions (laughs).
Nakahara:
No, but I’ll be in trouble if you don't tell me (laughs).
Tateishi:
When I was put in charge of R&D, my first impression was that everything was being done properly. If there are students who want to work in R&D, please come to ROHM. We do real R&D to get to the bottom of things.
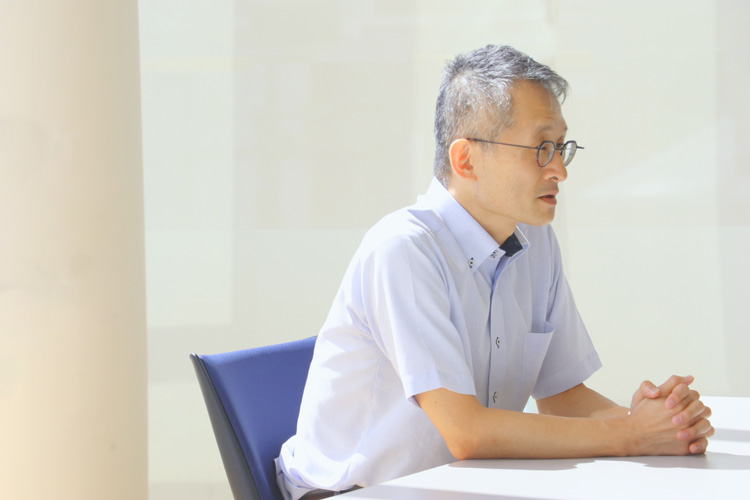
The nail that sticks out gets hammered down
Nakahara:
When I give lectures at universities, I always first ask students, ‘Don’t you think that semiconductors are pretty boring?’ Living in Japan, I got the feeling that semiconductors are not very exciting. But in fact nothing could be further from the truth. And the semiconductor market has only continued to grow. So I tell them, ‘If you don’t join the semiconductor industry, you’ll lose out.’ I also tell students that if they are serious about their work, I think ROHM is a good choice.
Tateishi:
ROHM has a corporate culture of ‘not hammering the nail that sticks out.’ We believe in developing individual abilities to the fullest.
Nakahara:
If you seek a safe path, ROHM may not be the best fit. But if you want to accomplish something, maybe give ROHM a try.
Tateishi:
I joined ROHM as a mid-career hire in 2014. When I first joined the company, I felt that the range of tasks assigned to each employee was wide. The business division in particular is quite broad.
Nakahara:
ROHM likes all-rounders.
Tateishi:
That’s right. But we’re trying to find the right balance. Until now, there has been a strong tendency to leave everything to the person in charge. Of course, you need people who can do everything, but at the same time, it is important to have people with specialized expertise. Therefore, we introduced the specialist position system in 2019. The position includes not only technical, but also IT and legal work. This system allows us to properly evaluate those who have chosen a career path that focuses on a special field. For more advanced engineers, we have prepared the next steps, such as ‘Fellows’ and ‘Senior Fellows’, with plans to appoint about 10 Fellows over the next 5 years. We offer professional development options as a career plan. The specialist position is term-based for a period of 4 years, and this year we have come full circle. The position will be reselected at the end of the term, where we plan to certify to near capacity.
Change in the Number of Specialist Appointments (Cumulative)
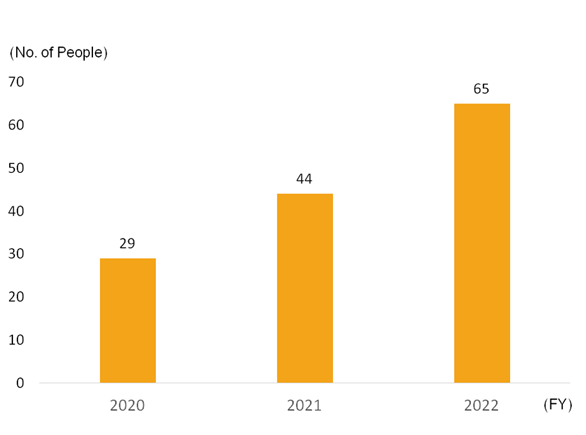
Application trends by area of expertise
Nakahara:
Mr. Tateishi, how do you feel about the reaction of employees to the specialist position?
Tateishi:
While operating the system, we noticed that we tend to receive more applications from people in the LSI field than from the discrete sector. I think this is because when comparing LSI and discrete development methods, we noticed that LSI entails a hierarchy of work one level deeper. With LSI, the circuit is placed on top after establishing the manufacturing process. But for discretes, the manufacturing process itself determines the structure of the device. This situation results in LSI having more people with expertise.
Nakahara:
The LSI industry is tightly divided into separate fields, with each field requiring a high degree of specialization. In contrast, with discrete devices one engineer can be in charge of everything from wafers to the final product. For this reason, there will be more people who aim to become all-rounders than specialists, capable of doing everything themselves. So I believe that there will be a difference in the number of applicants for specialists.
Personnel evaluations that don’t depend on luck
Nakahara:
When evaluating people involved in R&D, the difficult part is the research theme, since luck plays a role in terms of whether or not we can get to the commercialization stage.
So I try to evaluate using two types of outputs. One is a technical report. This is a summary of the results of research usually worked on for a certain period of time. The other is external publications such as patents and academic papers. Since this includes external evaluation, greater importance is placed on this than the technical report. These outputs confirm whether the research is proceeding based on systematized logic while maintaining background data. Commercialization is irrelevant. As long as the outputs are submitted, a certain amount of recognition will be received.
However, the effects of luck (good or bad) cannot be ruled out. Therefore, I carefully review each research theme with the researcher’s supervisors, and if I find that a theme does not have a high future potential, I may encourage the researcher to change the course of their research.
Tateishi:
Naturally, good and bad luck also exist in the business division, so it must be taken into account in personnel evaluations. I simply believe we should give promotions/advancement based on ability and bonuses for results. Reward those who have accomplished great achievements with bonuses when evaluated on a semi-annual or annual basis. As for promotions and advancement, I think they should be based on ability, not results, as there is a fair amount of luck involved in the theme.
By developing career paths that allow engineers to grow while improving their compensation, they will be able to focus on research. At ROHM, we have created a climate that allows engineers to shine. For sustainable growth, we will need even more diverse human resources than ever before, so I hope to have new graduates, and career hires, to join our ranks.
3.ROHM R&D Features
-Continuing to focus on R&D for the benefit of the world-
In corporate R&D, where business growth is required, the efficiency of investments is always a matter of debate. Many of the central research labs established by companies in the past have now been abolished, partly because they focused on basic research. We asked Mr. Tateishi and Mr. Nakahara to discuss investment efficiency in R&D and the portfolio management of research themes.
Nakahara:
The most important purpose for corporate R&D is to be useful to the world. So the theme must be based on that. It is often pointed out that R&D is an inefficient investment. However, that is because we often select themes based on the viewpoint of seeds, where both the technology and themes are interesting. Instead, investment efficiency can be improved by considering themes from the viewpoint of what can be of use to the world.
Tateishi:
From a management perspective, we are sometimes asked, ‘What is the most important thing in R&D?’ As Mr. Nakahara pointed out, it is important for research in a company to produce results, but R&D has a certain aspect of gambling. Themes with a high probability of success generate small returns, while themes with low probability generally yield high returns. Management should keep this in mind.
In other words, it is better to have a large number of themes with a high probability of success. At the same time, it is okay to have a theme with a low success rate but a very high return if successful. But we shouldn’t take on themes with high risk and low return. If sufficient returns can be secured from a combination of these themes, we can say that the R&D is well-managed.
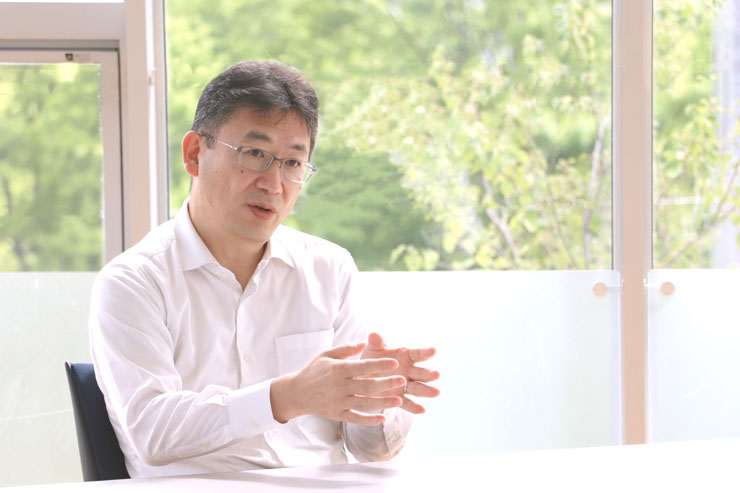
Aiming for a batting average over 30%
Tateishi:
In the first place, it’s impossible to achieve success with all themes. What's more, it is quite difficult to get a big hit.
Nakahara:
I agree. ROHM’s R&D Center is also working on themes close to our business, so if you include those, I think we have about a 50% success rate. A venture capitalist I know said a success rate of just 10% is sufficient.
Tateishi:
Because one may swell to more than 10x the total investment.
Nakahara:
Exactly. R&D could use this level of awareness. In other words, a batting average of 10%. But we’re not going to stop at 10%. I want to go for over 30% (laughs).
Tateishi:
I wonder how difficult that would be (laughs).
Nakahara:
I think we can achieve this if we do a good job of managing our portfolio of research themes. Certainly, it is impossible to go over 30% with high-risk themes alone. But 10% is fine. It’s not impossible if we combine this with low-risk low return themes.
Application-side research is also important
Nakahara:
The R&D Center is also working on research areas close to applications. For example, in the power field, ROHM has been specializing in device manufacturing, then around 2015 began research on the application side. This has now become a trend at ROHM, and we have become relied upon by each department. This is also one of the successes.
Tateishi:
When thinking about R&D, I believe there are two kinds of stories, the story before the card is turned and the one after the card is turned. In other words, the story in which the world has not yet recognized the practical possibility, and the story where the road to practical application is in sight. In the story after the flip, ROHM’s R&D is basically winning. This is due to the remarkable achievement that is SiC. In fact, the costs invested in R&D can be recouped by the returns from SiC alone.
So what about the story before the flip? I honestly don’t know. There are a number of relatively small themes before flipping over. For example, support technology in the power sector. It’s a little different from what is commonly referred to as R&D, but I think this kind of approach is important. However, if we start aiming for a high batting average, the number of themes with relatively small returns will increase in the future. That’s why it’s a good idea to have some home run themes in your portfolio.
Nakahara:
As someone who manages R&D, I’m trying to get more hits, even if I can’t say that they’re all home runs. But some of the themes will have a fairly large return if hit.
Get on base even if it’s ugly
Tateishi:
I think ROHM’s R&D selects themes based on technology marketing. Technology marketing here refers to the optimal allocation of themes within four quadrants, each of which is a multiplication of existing and new technologies and markets, respectively (Fig. 2). We use this as a guideline for selecting themes.
[Figure 2. Resource Allocation at ROHM’s R&D]
![[Figure 2. Resource Allocation at ROHM’s R&D]](/documents/11303/12030951/img_03.jpg/007b874f-af4f-e769-b155-84e9d6faacd4?t=1694501387863)
Nakahara:
What I would like to say to shareholders and investors is that ROHM is not working on interesting technological themes, but on themes that are useful to society.
Looking around the world, I think that there are still many R&D themes that companies are working on because they are interesting. Such studies may occasionally hit, but there many strikeouts. However, even if you get on base with a bluff infield hit, you can steal bases and get home with a quick hit. This results in a score. Getting a score means being useful to society. At any rate, the point is to get on base and continue to focus on R&D that is useful to the world. That is ROHM R&D’s approach.
At a time when it is difficult to predict the future, we will continue to inspire ourselves to actively enjoy the challenge of the unknown while contributing to society by creating world-leading products.
【PROFILE】
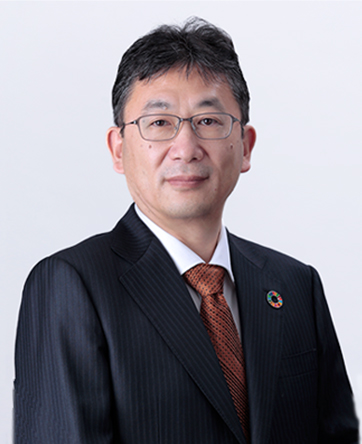
Director, Senior Managing Executive Officer ROHM Co., Ltd.
Tetsuo Tateishi
Obtained a master’s degree from Kyoto University in March 1987. Engaged in LSI development at an equipment manufacturer and semiconductor supplier. Joined ROHM in July 2014, where he oversaw advanced technological development for power supply ICs. Led the development of ROHM’s Nano Series utilizing leading-edge power supply technology. Became a Fellow in charge of technical development at the LSI Development Division in February 2019. Assumed his current position in June 2019 after working as Director and General Manager of the LSI Development Division.
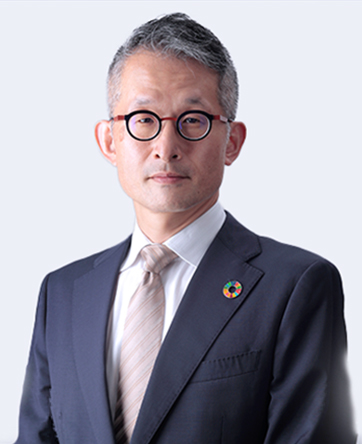
General Manager, R&D Center, ROHM Co., Ltd.
Ken Nakahara
Joined ROHM in 1995. Involved in the development of gallium arsenide (GaAs) laser diodes, zinc oxide (ZnO) LEDs, and gallium nitride (GaN) power devices. Appointed Director of the R&D Center in 2019, where he has been spearheading research on new material devices, power devices and systems, simulation technology, and much more.Became an IEEE Senior Member in February 2021.
Nakahara:
The main reason for soliciting research from universities and other organizations is that they approach R&D from a different perspective than companies. Universities conduct research with a genuine desire to know or investigate something as the driving force. But even if the results of do not always match what companies are looking for, there is always wisdom to be gained.
On the other hand, as companies are focused on commercialization and making a profit, they tend to pay little attention to the ‘why’ and ‘how’ and instead think that if you know how to make it (manufacturing method), why not do it? Therein lies the catch. For example, quality assurance requires an understanding of the ‘why’ (the essence), but companies often pass it off as, ‘It's ok, since we have a proven track record’, or ‘It's ok because we have tested it.’ We believe that the in-depth knowledge gained by universities and other institutions will be of great help in understanding this essence.